When it comes to high-volume cutting, you need a wheel that cuts fast, lasts a long time, and brings a high level of safety. You need the hardest working cutoff wheel on the market. Metal workers know that angle grinder cutoff wheels aren’t an area you can afford to skimp on. Flexovit knows this as well, which is why we’ve spent over 20 years refining our Razorblade line of thin cutoff wheels to optimize value and improve your bottom line. Razorblades are our most popular wheel, and with good reason.
What are Razorblade Wheels?
The Razorblade line is a series of thin cutoff wheels for use with angle grinders. The Razorblade line includes seven variations, each intentionally designed to meet a different set of needs.
● Razorblade, for long life
● Razorblade EZ, for fast cutting
● Razorblade HD, for heavy duty use
● Razorblade 27 SS, for free cutting on stainless steel
● Razorblade ALU, for load free cutting on aluminum
● Razor Thin, thin profile for narrowest kerf
● Razor Combo, for cutting, deburring and light grinding
Razorblade wheels were all designed with extra durable bond formulations, and for fast cutting action with narrow kerf.
What makes Razorblade wheels so great? Flexovit has devoted decades to research and improvement in three key areas: value, safety, and quality.
The Most Bang For Your Buck
Razorblade cutoff wheels comes in both Type 1 (flat) and Type 27 (depressed center). There are product options available for cutting all ferrous metals, stainless steel and aluminum (as well as non-ferrous metals like bronze and copper). They’re available in sizes from 4” to 7”, and are available in seven specifications. In short, Razorblade wheels are amazingly versatile, offering options that suit a wide variety of needs and applications.
What makes Razorblade wheels the best value isn’t just their versatility and flexible product offerings, though. We’re confident that our wheels will outperform any other wheel on the market. In fact, we challenge you to come in and see for yourself with our P.A.C.E. Challenge.
Below is real data from past P.A.C.E. Challenges, in which a Flexovit Razorblade wheel performed in head-to-head matchups with various competitor products. In these tests, plunge cuts were made until the point at which the flange did not allow a complete top-to-bottom cut due to wear on the wheel.
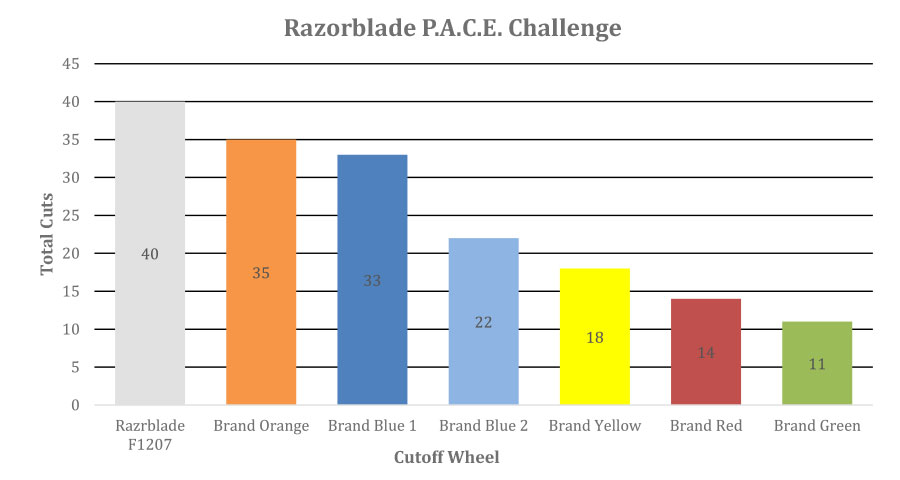
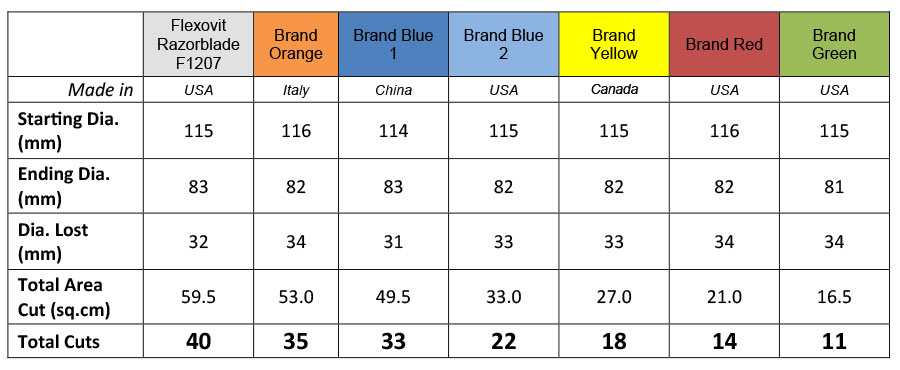
*Plunge cuts on ½” Sch 40 pipe (area 1.5 sq.cm per cut) at 10 amps.
**All wheels are 4 ½” x 7/8” Type 1 thin cutoff wheels
Razorblade wheels consistently deliver the most work per penny, making the most cuts before wearing out. We know that changing and mounting new wheels is a hassle that takes several minutes each time, so we design all our wheels to last longer than competing products.
The Safest Construction
When you have a wheel spinning at high RPM’s, safety is your top priority. If that wheel cracks, it quickly disintegrates, scattering dangerous wheel fragments at high speed. Of course, workers should always take proper safety precautions including wearing protective eyewear and clothing, using proper safety guards on power tools, respecting maximum RPM ratings marked on the wheel, and other precautions consistent with ANSI Code B7.1. But isn’t it better to also use wheels whose safety features are the best on the market?
Resinoid-reinforced cutoff wheels, including Razorblade wheels, are constructed with fiberglass to prevent them from breaking. In order for the fiberglass to bond with the wheel matrix, it must be coated with phenolic resin before inclusion in the wheel. Since the resin coating gets drier with time, it is important that the coated and cut fiberglass is used within a certain time frame. Most manufacturers buy pre-coated, precut fiberglass for inclusion in their wheels. However, Flexovit coats and cuts the fiberglass at our plant as part of our manufacturing process. This means that the fiberglass is always freshly coated, which creates a more unified bond with the matrix of resin and grain when the wheel is produced. Because we have more control over this process, our fiberglass reinforcement gives the wheel strength to resist centrifugal and side load forces. It boils down to this: freshly-coated fiberglass creates a better bond, which results in a safer product. With in-house fiberglass coating and cutting, Flexovit maintains a significantly higher degree of quality control when it comes to the safety and performance of our grinding wheels.
USA Made For Controlled Manufacturing
We also maintain a high degree of control over the rest of our production processes. Razorblade wheels, like all Flexovit resin-bonded wheels, are made right here in the United States. And that’s important, because it means we retain control over every aspect of production. Our raw materials are sourced domestically, and all of our production happens in-house. We’re proud to be a USA manufacturer who supports other USA manufacturers. Flexovit Razorblades are made without compromise in the USA.
Flexovit is committed to following strict manufacturing standards and safe product use, and these standards are carried into each and every one of our production processes. Flexovit’s Quality System is ISO certified, so you can count on every item being produced in exactly the same way, with the same results.
The Longest Lasting, Hardest Working Cutoff Wheel You Can Buy
Razorblade wheels offer the longest life in the toughest applications. They’re an essential tool in any metalworking facility that consistently outlast, out-cut, and outperform other wheels on the market.